Our Services
Has it been a while since you had your equipment inspected? Do you perform regular maintenance checks to ensure your equipment is in safe working condition?
Contact IBSI today to Schedule an inspection!
- Pilot and Ignition Systems: Regular inspection and maintenance of pilot lights and ignition systems to ensure they function properly.
- Fuel Supply: Verification of the fuel supply system, including piping and control valves, to prevent leaks and ensure proper fuel flow.
- Temperature Controls: Calibration and testing of temperature control systems to maintain safe operating temperatures and prevent overheating.
- Ventilation and Combustion Air: Adequate ventilation and combustion air supply to support combustion without creating hazardous conditions.
- Flame Monitoring: Checking flame sensors and monitoring systems to ensure reliable detection and supervision of the flame during operation.
- Interlock Systems: Ensuring proper functioning of interlock systems that prevent unsafe conditions by coordinating various elements of the heating system.
- Pressure Relief Devices: Inspection and testing of pressure relief devices to prevent excessive pressure buildup within the system.
- Electrical Systems: Verifying the integrity of electrical components and systems associated with the furnace or oven.
- Training and Documentation Providing adequate training for personnel operating the equipment and maintaining comprehensive documentation of safety checks and procedures.
It's important to note that the specific safety checks may vary depending on the type of industrial furnace or oven and the processes involved. Users should always refer to the latest edition of NFPA 86 for detailed guidelines and compliance requirements.
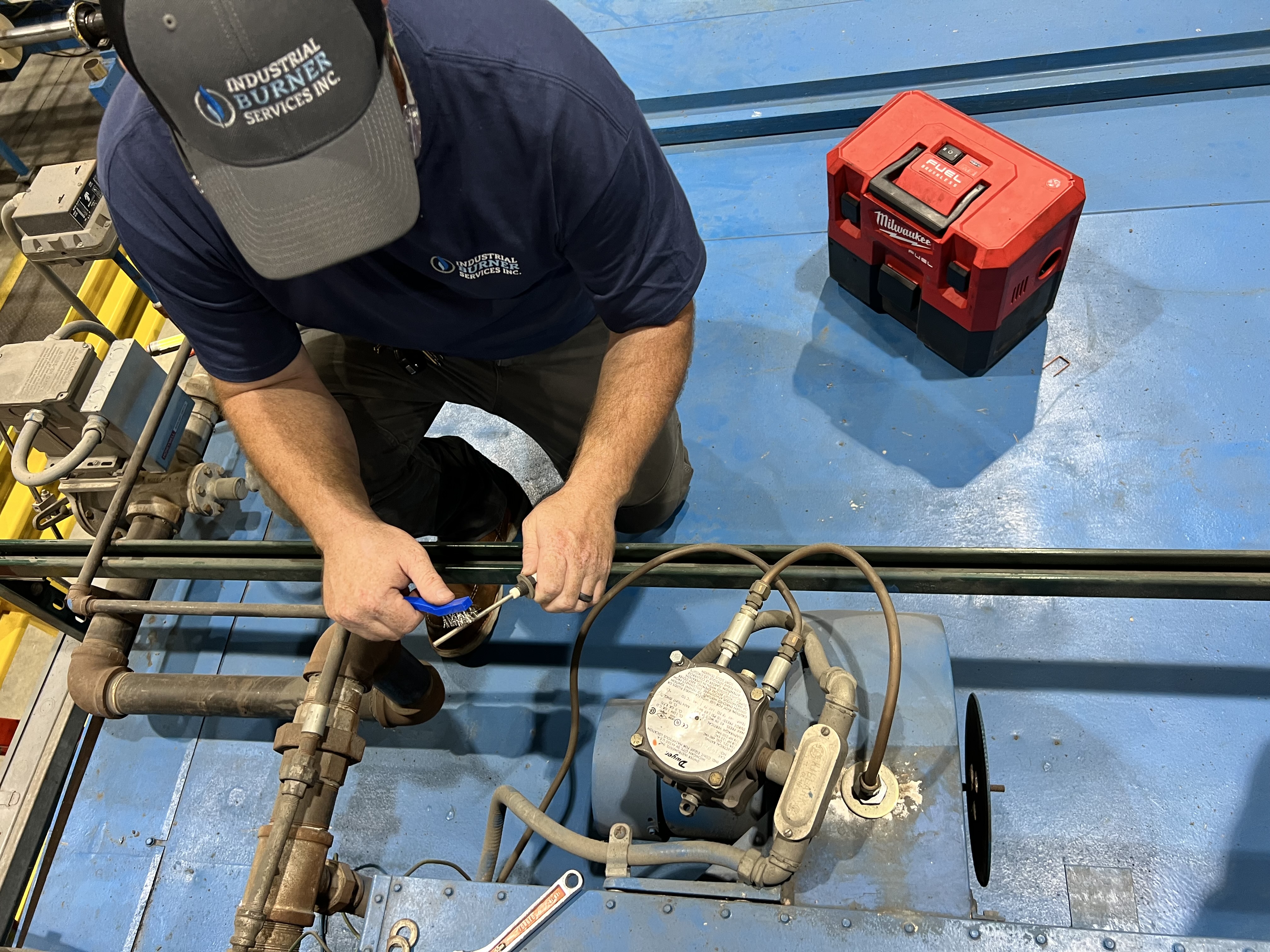
Does your maintenance team know how to properly inspect burner systems and determine if parts need to be replaced or repaired?
Contact IBSI today to Schedule an inspection!
- Scheduled Inspections: Regular inspections of equipment and machinery are conducted at predetermined intervals. This involves checking for signs of wear and tear, loose components, leaks, or any other issues that may impact performance.
- Routine Maintenance Tasks: Performing routine tasks such as lubrication, cleaning, and calibration to ensure that equipment operates efficiently. This helps prevent issues related to friction, dirt accumulation, and inaccurate measurements.
- Replacement of Worn Parts: Identifying and replacing parts that are showing signs of wear or are reaching the end of their lifespan. This proactive approach helps avoid unexpected breakdowns.
- Documentation and Record-Keeping: Keeping detailed records of maintenance activities, including inspection reports, repairs, and replacements.
- Training and Skill Development: Ensuring that maintenance personnel are adequately trained to identify issues, perform routine maintenance tasks. Skilled personnel are essential for the success of preventative maintenance programs.
- Emergency Response Planning: While the focus is on preventing issues, having a well-defined plan for responding to unexpected breakdowns is crucial. This includes having spare parts on hand, a rapid response team, and contingency plans to minimize downtime.
Implementing a robust industrial preventative maintenance program can lead to several benefits, including increased equipment reliability, extended equipment lifespan, reduced downtime, improved safety, and overall cost savings for the organization.
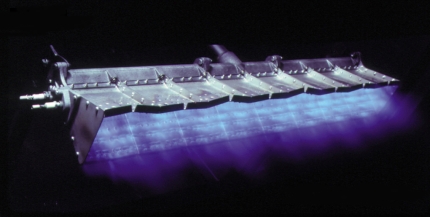
Do your burners light reliably and maintin a proper flame signal?
Contact IBSI today to Schedule an inspection and burner tuning!
The key aspects of burner tuning include:
- Air-Fuel Ratio Adjustment: Achieving the right balance between the amount of air and fuel supplied to the burner is essential for optimal combustion. A proper air-fuel ratio ensures complete combustion, reducing the formation of harmful byproducts like carbon monoxide and unburned hydrocarbons.
- Flame Stability: Ensuring a stable and consistent flame is crucial for reliable operation. Burner tuning involves adjusting parameters to maintain a steady and well-defined flame, preventing flameout or erratic combustion.
- Combustion Efficiency: Maximizing combustion efficiency helps in utilizing fuel more effectively and reducing waste. Tuning involves optimizing combustion conditions to achieve the highest possible efficiency.
- Emissions Control: Regulatory standards often dictate the permissible levels of emissions from industrial processes. Burner tuning plays a significant role in meeting these standards by minimizing the release of pollutants into the atmosphere.
- Heat Transfer Optimization: Proper burner tuning contributes to efficient heat transfer from the combustion process to the intended application, whether it's in a boiler, furnace, or another system.
- Equipment Longevity: Tuning the burner helps in preventing issues such as overheating, corrosion, and premature wear, thereby extending the lifespan of the equipment.
Regular maintenance and periodic tuning are essential to keep burner systems operating at peak efficiency and in compliance with environmental regulations.
Do you need to upgrade your system to improve efficiency, reliability and safety?
Contact IBSI today to Schedule an inspection!
- Assessment and Analysis: The upgrade process begins with a comprehensive assessment of the existing combustion system. The goal is to identify areas where improvements can be made, whether in terms of energy efficiency, emissions reduction, NFPA safety requirements or overall system reliability.
- Burner Upgrades: Upgrading burners can involve replacing or retrofitting existing burners with more advanced models. This could include low-emission burners, high-efficiency burners, or burners designed for specific fuel types. Improved burner technology enhances combustion efficiency, reduces emissions, and allows for greater flexibility in fuel options.
- Control System Modernization: Modernizing control systems involves upgrading sensors, actuators, and controllers to more advanced and precise technologies. Upgraded control systems contribute to better regulation of combustion parameters, leading to increased system reliability, safety, and operational flexibility.
- Fuel System: Upgrades to the fuel system may involve improving fuel delivery mechanisms, upgrading fuel nozzles, or adopting technologies for better fuel atomization. Optimizing the fuel system ensures more efficient combustion, reducing fuel wastage and improving overall system performance.
- Instrumentation and Monitoring: Enhancing instrumentation involves upgrading sensors and monitoring devices to provide more accurate and real-time data on combustion conditions. This may include the adoption of advanced thermal imaging or gas analyzers. Improved instrumentation allows for better control and optimization of combustion parameters, leading to increased system efficiency and reliability.
- Safety System Upgrades: Safety systems may be upgraded to incorporate advanced flame detection technologies, emergency shutdown mechanisms, or other safety features. Ensuring the highest level of safety is critical, and upgraded safety systems contribute to the prevention of accidents and the protection of personnel and equipment.
- Compliance with Standards: Upgrades often include modifications to ensure compliance with the latest industry standards, regulations, and environmental requirements. Adhering to standards ensures that the combustion system meets legal and regulatory obligations, providing a foundation for sustainable and responsible operation.
Combustion system upgrades are a strategic investment for industries aiming to improve efficiency, reduce environmental impact, and extend the life of their equipment. These upgrades not only enhance the performance of combustion systems but also contribute to overall operational excellence and sustainability.
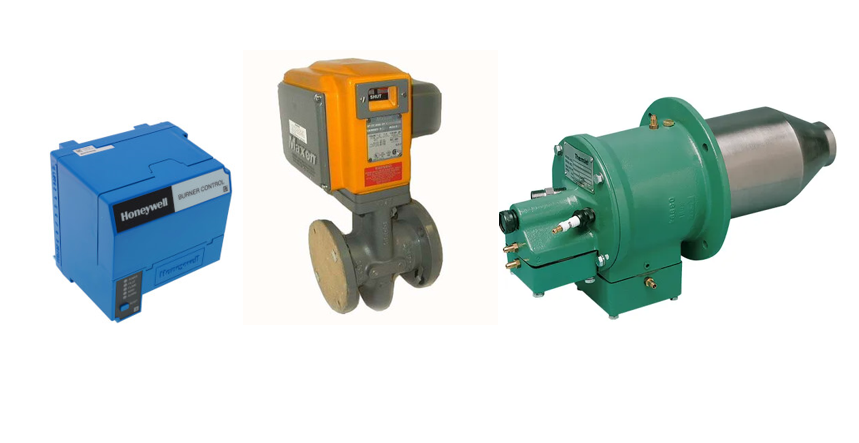
IBSI provides engineering support to determine the right parts for your needs. Our technicians can install parts and test and tune for proper operation. IBSI can supply all of the major brands of parts.
Contact IBSI today to get a quote!
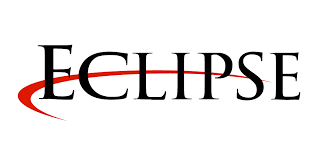
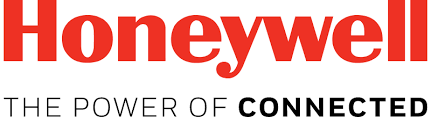
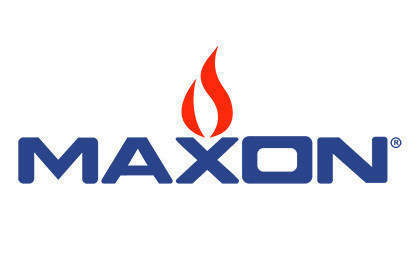
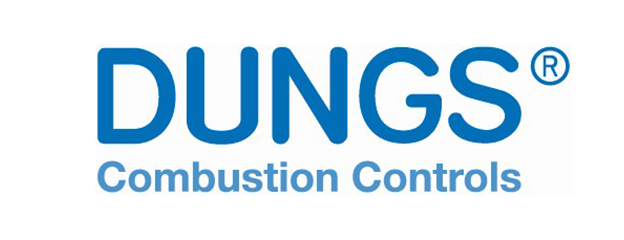
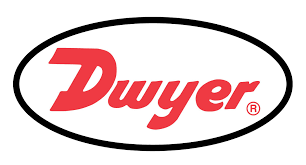
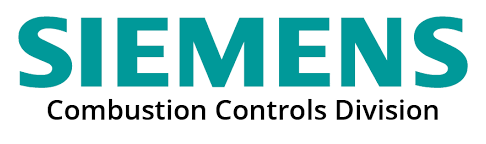
- Burners:
- Burners are devices that mix fuel with air and ignite the mixture to produce a controlled flame. They are responsible for creating a stable and efficient flame within combustion chambers.
- Igniters:
- Igniters are components that provide the initial spark or flame required to ignite the fuel-air mixture in the combustion process. Igniters are critical for the startup phase of combustion systems, ensuring a reliable ignition source for the burners.
- Combustion Controls:
- Combustion control systems include sensors, controllers, and actuators that regulate the fuel and air supply to maintain optimal combustion conditions. These controls ensure that the combustion process operates within specified parameters, adjusting fuel-air ratios and other variables for efficiency and safety.
- Flame Detectors:
- Flame detectors are safety devices that monitor the presence or absence of a flame in the combustion chamber. Flame detectors help prevent unsafe conditions by detecting flame failure or irregularities, triggering safety measures such as shutting down the fuel supply.
- Valves:
- Valves control the flow of fuel, air, and other fluids within the combustion system. Types include control valves, safety valves, and shut-off valves. Valves regulate the supply of fuel and air to maintain precise control over combustion conditions, and they provide safety measures in case of system malfunctions.
- Sensors and Instrumentation:
- Sensors measure various parameters such as temperature, pressure, and gas concentrations within the combustion system. Instrumentation provides real-time data to control systems, allowing for adjustments to optimize combustion efficiency and meet performance requirements.
These combustion system parts work together cohesively to create a controlled and efficient combustion process. Their proper design, selection, and maintenance are essential for achieving reliable and sustainable performance in a wide range of industrial applications.

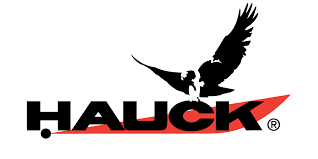
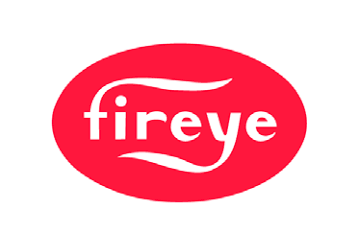


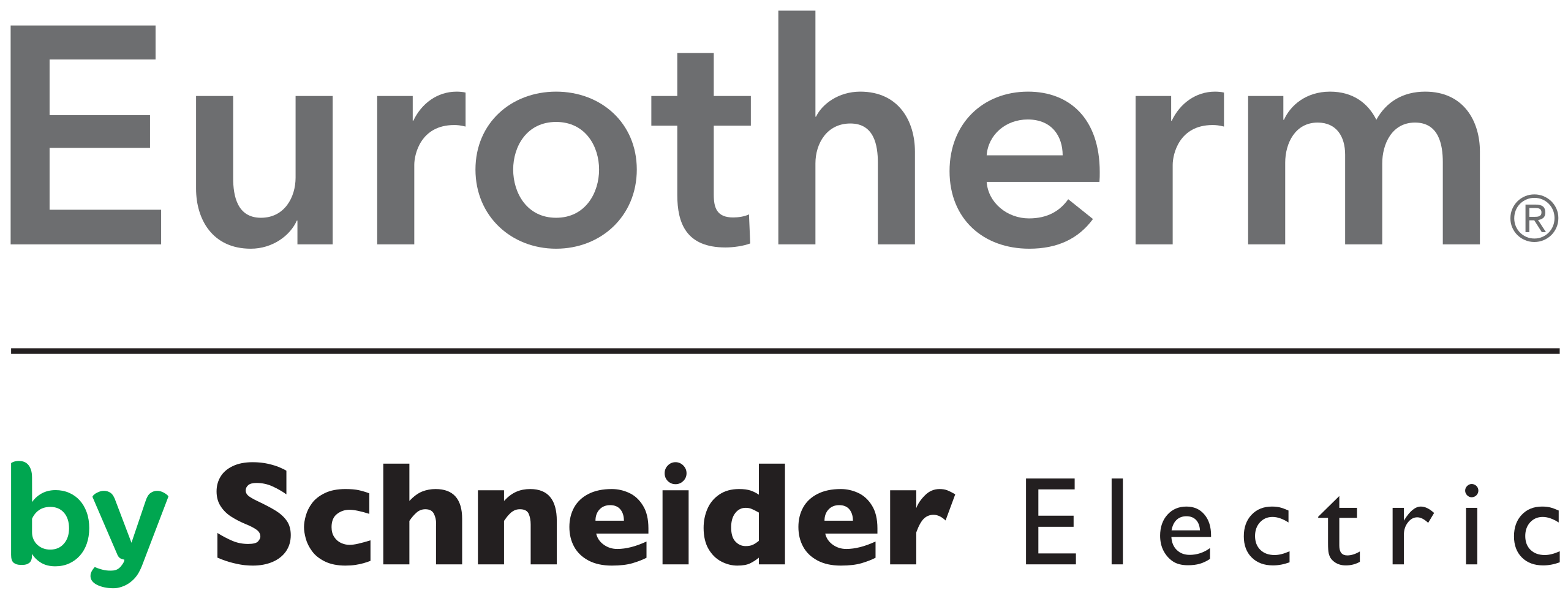
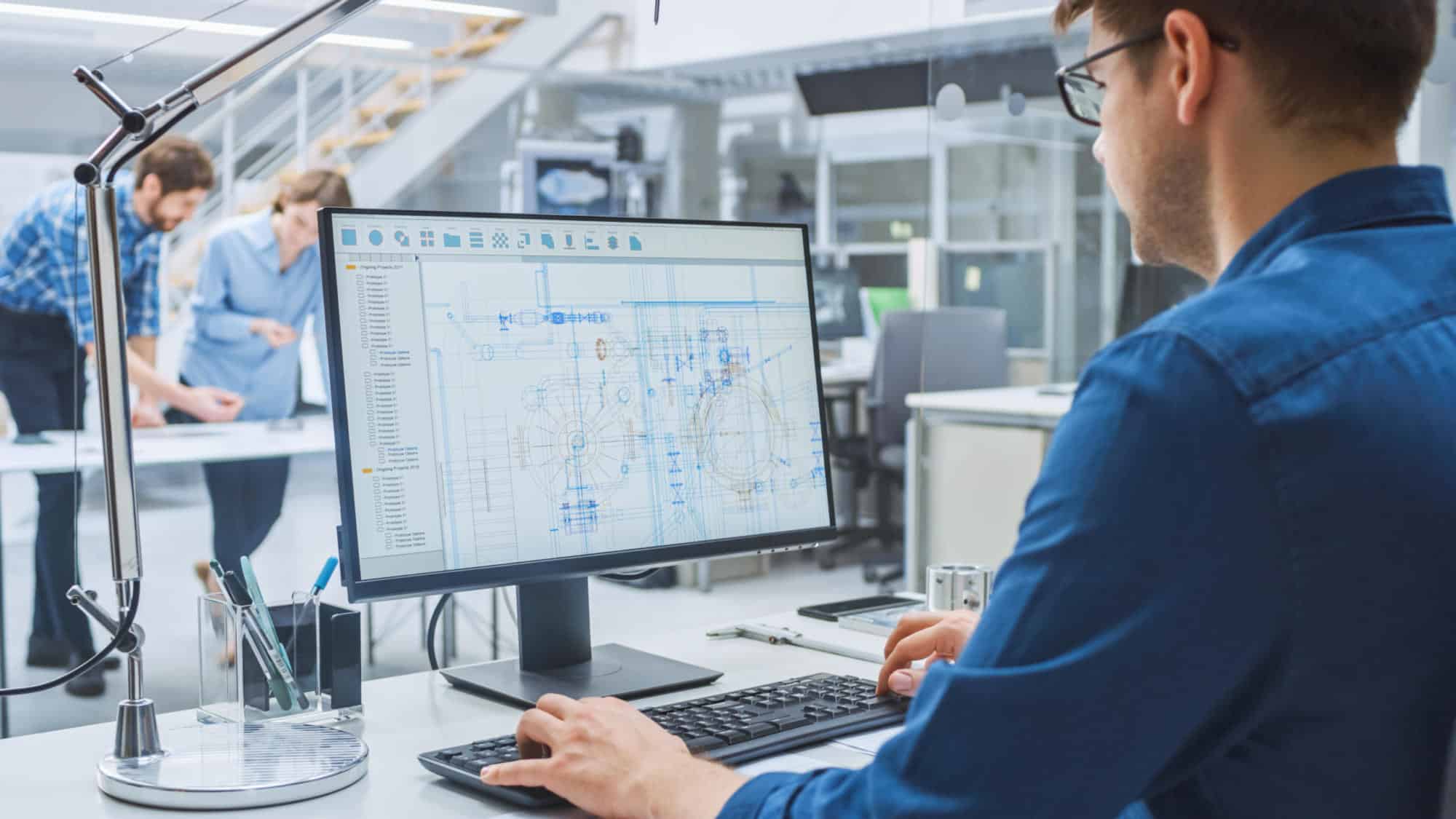
IBSI's engineers can provide a turnkey solution including design, drawings and fabrication.
Contact IBSI today to discuss what you need!
- Our engineers will collaborate with you to define the scope of your project, ensuring that your combustion systems meet all safety standards and regulatory requirements.
- Preliminary drawings are created and provided to the customer for review
and approval. Typical drawings included are:
- Wiring diagram
- Panel Layouts
- P&ID
- Mechanical
- Our engineers oversee fabrication and assembly to ensure it is going as planned.
- Upon completion, "As-Built" drawings are updated if any design changes were made during fabrication.
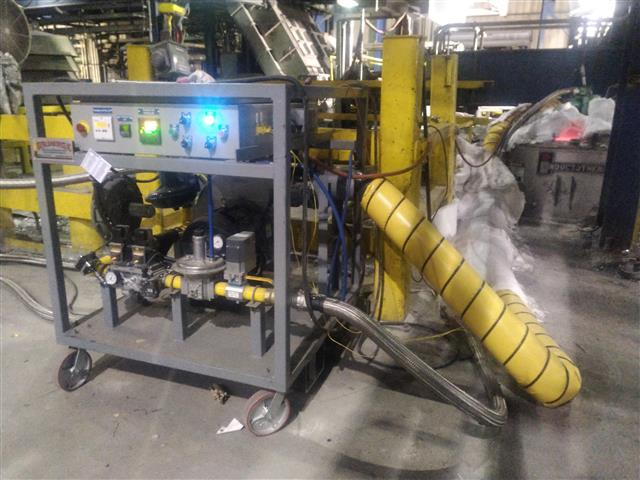
IBSI's engineers can provide a turnkey solution including design, drawings and fabrication.
Contact IBSI today to discuss what you need!
- Design: Developing detailed drawings that outline the dimensions, materials, functionalities, and performance specifications of the equipment.
- Manufacturing: Utilizing specialized tools, machinery, and techniques to fabricate the components according to the design specifications. This may involve various processes such as welding, machining, casting, and assembly.
- Customization: Tailoring the equipment to meet specific operational requirements, environmental conditions, regulatory standards, or ergonomic considerations.
- Testing and Validation: Conducting rigorous testing and validation procedures to ensure that the custom equipment meets performance standards, safety requirements, and reliability expectations.
- Documentation: Providing comprehensive documentation that includes technical drawings, operation manuals, maintenance instructions, and certification records as applicable.
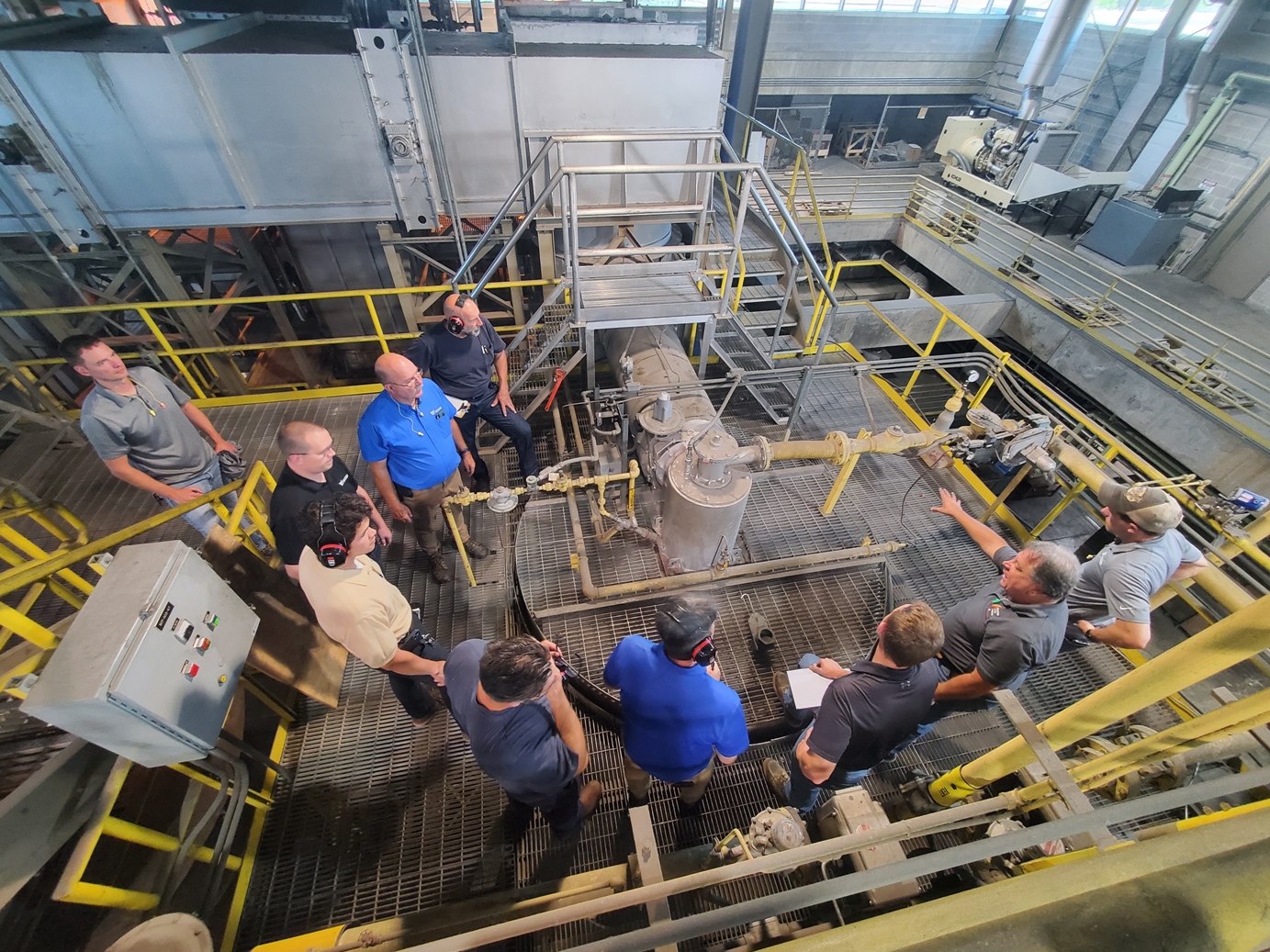
IBSI can provide combustion training tailored to your specific equipment. With a combination of classroom and hands on training, your personnel will become knowledgable and comfortable working on your equipment.
Contact IBSI today to get a quote for training your team!
- Fundamental Principles: Participants in burner system training gain a solid understanding of the fundamental principles of combustion and the impact of air-fuel ratios on efficiency.
- Safety Protocols: Emphasis is placed on safety protocols and procedures related to burner system operation. This includes knowledge about handling fuel sources, ignition systems, emergency shutdown procedures, and the use of safety equipment.
- Components and Equipment: Training covers the various components of burner systems, such as burners, fuel delivery systems, combustion chambers, and control panels. Participants learn how these components work together to achieve optimal combustion.
- Operation and Control: Participants are trained on the operation and control of burner systems. This involves understanding the functions of control panels, adjusting settings for different operating conditions, and monitoring key parameters to ensure efficient performance.
- Maintenance Practices: Training includes instruction on routine maintenance tasks essential for keeping burner systems in good working condition. This may involve cleaning, lubrication, inspection, and the replacement of worn-out components.
- Troubleshooting Techniques: Participants learn how to identify and address common issues and malfunctions that may arise during the operation of burner systems. Troubleshooting skills are crucial for minimizing downtime and ensuring continuous operation.
- Regulatory Compliance: Training covers relevant regulations and standards governing the operation of burner systems, ensuring that participants understand and adhere to industry-specific guidelines and compliance requirements.
- Hands-On Practical Exercises: Practical hands-on exercises are often a key component of burner system training. Participants have the opportunity to apply theoretical knowledge, gaining practical experience in operating and maintaining burner systems.
- Documentation and Reporting: Training includes instruction on maintaining accurate records, documenting maintenance activities, and generating reports. Proper documentation is essential for tracking system performance and compliance with regulatory standards.
Overall, burner system training aims to empower individuals with the expertise needed to ensure the safe, reliable, and efficient operation of burner systems in industrial settings. This training is valuable for operators, maintenance personnel, and anyone involved in the management of burner equipment.
Over time, refractory and insulation can degrade or come loose creating hot spots in your system. If your burner is not tuned properly, it also can cause hotspots that degrade, warp the combustion chamber causing hot spots.
Contact IBSI today to Schedule an infrared inspection!
- The primary goal of thermal imaging in burner systems is to identify and assess temperature variations across different components. This helps in detecting anomalies, optimizing efficiency, and preventing potential issues that may lead to equipment failure or safety hazards.
- Identification of Hotspots and Cold Spots: Thermal images reveal hotspots and cold spots in the burner system. Hotspots may indicate issues such as poor combustion, overheating components, or insulation problems, while cold spots may suggest insufficient heat transfer or cooling.
- Combustion Analysis: Thermal imaging can be used to analyze the combustion process by visualizing the temperature distribution within the combustion chamber. This allows for the optimization of air-fuel ratios and identification of combustion irregularities.
- Insulation Assessment: The thermal imaging of burner systems can help assess the effectiveness of insulation materials. Poor insulation may result in heat loss and reduced overall efficiency. Identifying areas with inadequate insulation allows for targeted improvements.
- Preventive Maintenance: By detecting abnormal temperature patterns early on, thermal imaging supports preventive maintenance efforts. Maintenance teams can address potential issues before they escalate, minimizing downtime and avoiding costly repairs.
Industrial thermal imaging of burner systems is a valuable tool for enhancing safety, optimizing performance, and supporting maintenance efforts. By visualizing temperature patterns, operators and maintenance teams can make informed decisions to ensure the efficient and reliable operation of burner systems in various industrial applications.
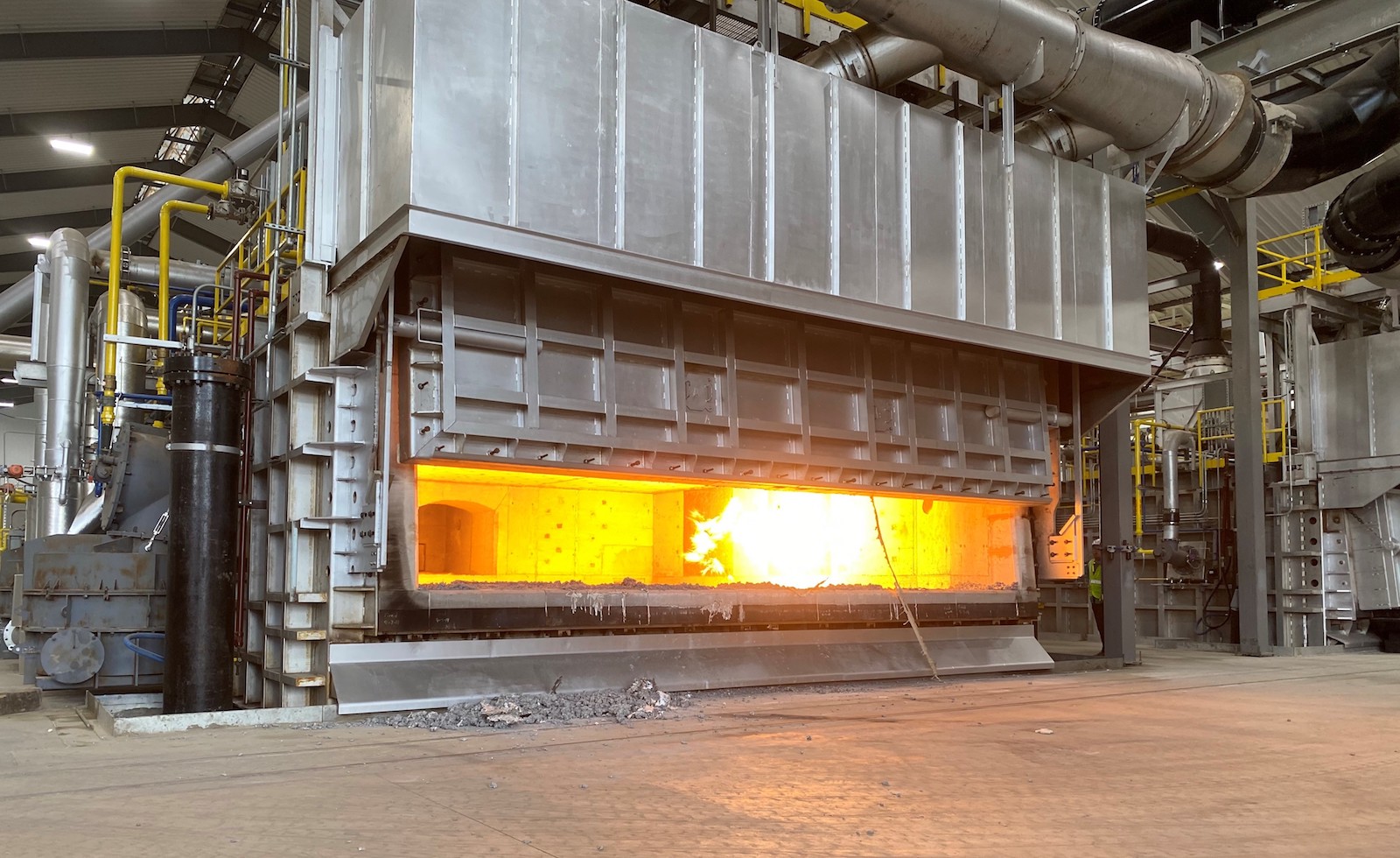
Contact IBSI today to get a quote!
- Preparation and Planning: The commissioning process begins with planning. This includes reviewing design documentation, developing a commissioning plan, and assembling a qualified team of engineers, technicians, and specialists.
- Functional Testing: The commissioning team performs functional testing to verify that each component and subsystem of the industrial equipment operates as intended. This includes checking electrical, mechanical, and control systems to identify and rectify any issues.
- Safety Systems Verification: Ensuring that safety systems, such as emergency shutdown procedures, alarms, and interlocks, are functional and in compliance with safety standards. This is a critical aspect of commissioning to prevent accidents and protect personnel.
- Training: Providing training for operators and maintenance personnel on the proper use, maintenance, and troubleshooting of the commissioned equipment. This ensures that the end-users are well-equipped to handle the equipment once it is in regular operation.
Industrial equipment commissioning is a collaborative effort involving various stakeholders, including engineers, project managers, equipment manufacturers, and end-users. The process is iterative, with adjustments made as needed to achieve optimal performance and reliability. Commissioning plays a crucial role in ensuring that industrial facilities operate safely, efficiently, and in compliance with regulatory standards.
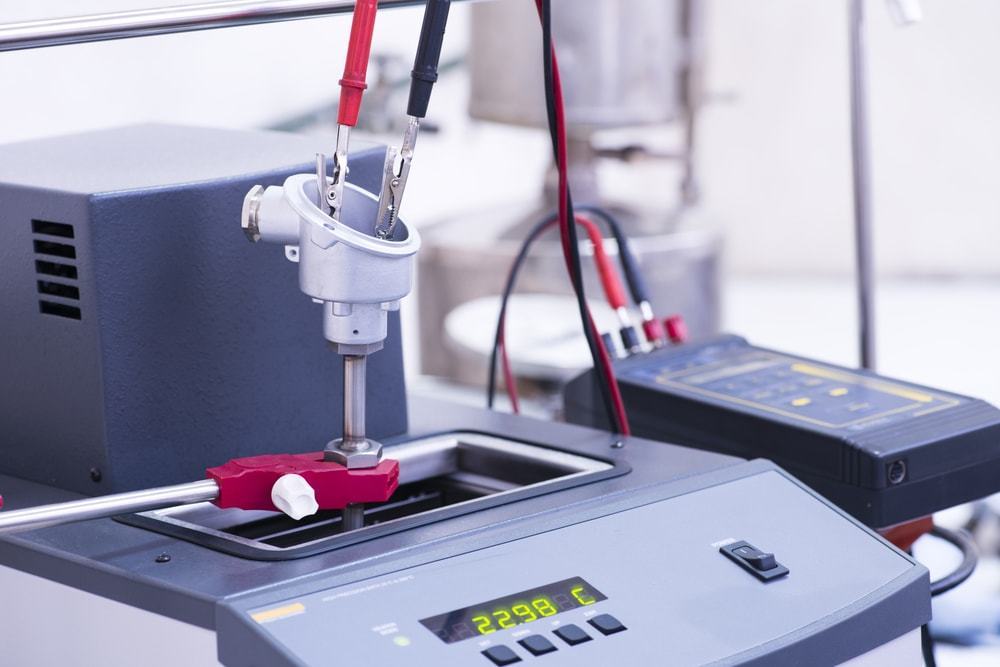
Often times thermocouples can fail and return misleading temperature readings.
Contact IBSI today to have your thermocouples tested!
- Certification: Ensuring that the thermocouple outputs accurate temperature readings when exposed to known temperatures. This involves comparing its readings against a known standard.
- Accuracy: Verification that the thermocouple meets specified accuracy requirements for its intended use. This may involve testing under various conditions to simulate real-world applications.
- Documentation: Providing documentation that details the results of calibration and testing, including any uncertainties or limitations in measurement.
- Compliance: Meeting relevant industry standards or regulations. Different industries or applications may have specific requirements for thermocouple performance.
Thermocouple certification is crucial in applications where temperature measurement accuracy is critical, such as in industrial processes, scientific research, and medical devices. It provides confidence that the thermocouple will provide reliable temperature readings within specified tolerances, helping to maintain process efficiency, product quality, and safety.